روان کاری و مشکلات ناشی از روان کار نامناسب چرخ دنده های صنعتی
به طور کلی چرخ دنده ها ممکن است در یکی از سه حالت روان کاری مرزی، مخلوط، و یا لایه ای کامل عمل کنند. روان کاری مرزی در هنگام حرکت یا توقف چرخ دنده های درگیر رخ می دهد.
کارکردن چرخ دنده ها به مدت طولانی در شرایط روان کاری مرزی سایش های سریع و سخت را به همراه خواهد داشت. با افزایش سرعت و حرکت نسبی چرخ دنده های رژیم روان کاری انها نیز به سمت روان کاری مخلوط حرکت خواهد کرد. با بررسی وضعیت تماس دو دندانه از دو چرخ دنده درگیر دیده می شود که تماس با حرکت لغزشی نسبتا بالا و حرکت غلتشی محدود آغاز می شود. با نزدیک شدن نقطه تماس به خط گام حرکت لغزشی کاهش می یابد. در روی نقطه خط گام حرکت فقط غلتشی است. بعد از عبور نقطه تماس از خط گام، حرکت لغزشی دوباره شروع می شود و تا نقطه اتمام درگیری دو دندانه شروع به افزایش می کند. ویسکوزیته روان کننده ها طی چرخه درگیری دندانه ها ثابت نمی ماند و با افزایش فشار به سرعت افزایش می یابد.در نواحی که فشار بالاست و تناوبی اعمال می شود، روان کننده ها به شکل مجازی شبیه به یک جسم سفت و سخت عمل می کنند.
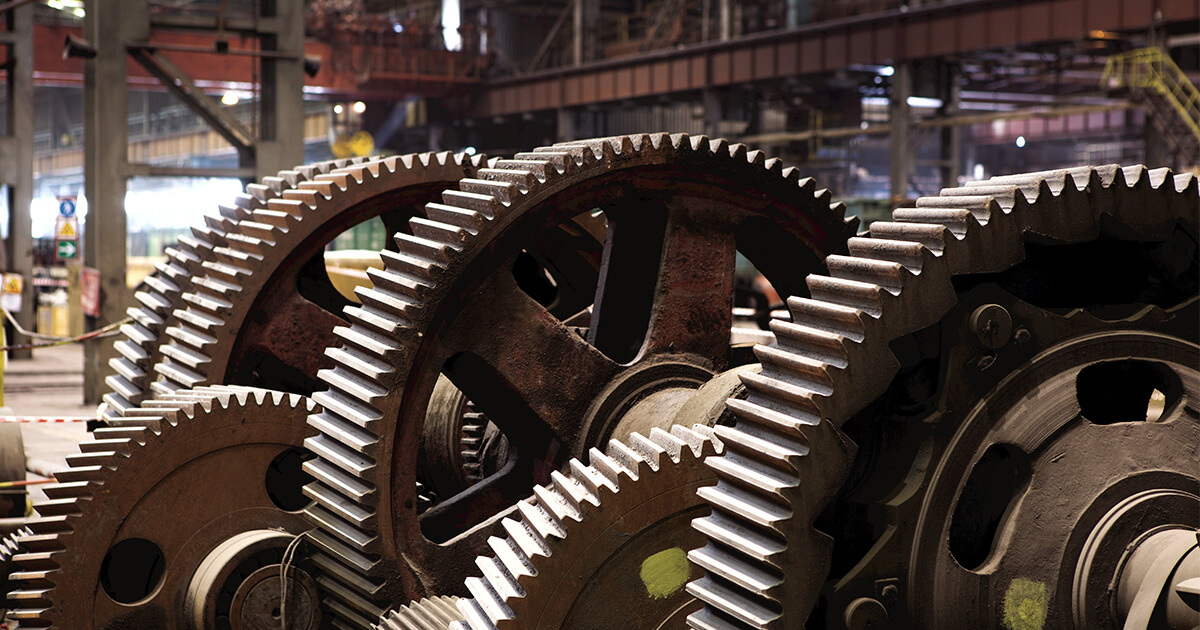
روان کننده های چرخ دنده
روان کننده های مصرفی در چرخ دنده ها باید قابلیت کاهش سایش، حفاظت در مقابل خوردگی و زنگ زدگی، مقاومت در برابر اکسیداسیون و تخریب شیمیایی، جلوگیری از تشکیل کف و جدا شدن آسان از آب را داشته باشند.به علت تنوع سیستم های اتقال قدرت چرخ دنده ای، روان کاری و نوع روان کننده های مصرفی در انها نیز منحصر به کاربرد های خاص شده است.
الف-روان کننده های حاوی مواد بازدارنده
این نوع روغن های معدنی حاوی بازدارنده های ضدزنگ و ضد اکسیداسیون هستند و ممکن است ترکیبات ضد کف و ضد سایش نیز داشته باشند.
ب-روان کننده های فشار بالا
این نوع روغن های باز دارنده حاوی مواد افزودنی فشار بالا نیز هستند. ترکیبات فشار بالا اصلاح کننده های اصطکاک اند و به دو نوع شیمیایی فعال و روان کننده های جامد تقسیم بندی می شوند. ترکیبات حاوی سولفور و فسفر از مواد شیمیایی و افزودنی های فعال اند. سولفور و فسفر در دماهای بالا با مواد موجود روی سطوح دندانه های چرخ دنده ها وارد واکنش می شوند و به راحتی یک لایه محافظت کننده نازک روی آنها تشکیل می دهند.
روان کننده های جامد دومین نوع از ترکیبات فشار قوی(EP) هستند. ذرات جامد(مانند گرافیت، مولیبدن ، بورات و ...)بین سطوح دو دندانه قرار می گیرند و از تماس فلز با فلز جلوگیری می کنند.اگر در یک سیستم انتقال قدرت، یاتاقان ها نیز به کمک سیستم روان کاری چرخ دنده ها روان کاری شوند باید این نکته اساسی را در نظر گرفت که، در صورت وجود برنز در یاتاقان ها، ترکیبات فشار بالای (EP) فعال نباید سبب بروز خوردگی آنها شوند. مواد افزودنی روان کننده جامد ممکن است سبب کاهش لقی ها و تلرانس های مجاز داخلی در قطعات دقیق و حساس(پوسته یاتاقان های دما بالا)، اعمال بارها و روز خرابی های احتمالی دیگر شوند.
ج-روان کننده های ترکیبی
این نوع روان کننده ها معمولا در موتور های بخار مصرف می شوند و مواد افزودنی آنها اسیدهای چرب با خاصیت کاهش اصطکاک اند. این نوع روغن ها عمدتا در چرخ دنده های محرکی که در دمای بالا کار می کنند مصرف می شوند.
د-روغن های ترکیبی چرخ دنده های باز
از این نوع روان کننده های بسیار سنگین برای روان کاری چرخ دنده های بزرگ که تحت بارهای سنگین و سرعت پایین کار می کنند استفاده می شود. این نوع روان کننده ها حاوی مواد افزودنی خاص اند که روغن ها را قادر می کنند استفاده می شود. این نوع روان کننده ها حاوی مواد افزودنی خاص اند که روغن ها را قادر می کنند به سطح دندانه ها بچسبند. این مواد هنگام تحت فشار قرار گرفتن و فشرده سازی به راحتی از محل درگیری دندانه ها خارج و تخلیه نمی شوند.
گریس کاری چرخ دنده
گریس روان کننده ای مایع است که ویسکوزیته آن به کمک سفت کننده های صابونی افزایش یافته است. صابون ترکیبات مایع را در خود نگه می دارد و در هنگام ضرورت آن را رها می کند. گریس ها فقط برای روان کاری در سرعت پایین و کاربردهایی که مقدار بار اعمالی پایین باشد مناسب اند. گریس ها به راحتی جریان نمی یابند و خاصیت خنک کنندگی شان نسبتا ضعیف است.
ویسکوزیته روان کننده های چرخ دنده
در انتخاب ویسکوزیته برای روان کننده های چرخ دنده باید به این موضوع توجه داشت که هر چه ویسکوزیته روان کننده ها بالاتر باشد، از دندانه های چرخ دنده ها در مقابل انواع صدمات بیشتر محافظت خواهد شد. با وجود این، مقدار ویسکوزیته روان کننده ها باید مشخص و در حد مجاز باشد تا از تولیدات گرمای زیاد، افت توان ناشی از نوسان شدید و تخریب ساختار مواد افزودنی آنها در چرخ دنده ها یا یاتاقان های با سرعت بالا جلوگیری شود. ویسکوزیته عمل کردی روان کننده ها را می توان با دمای عمل کردی چرخ دنده های متحرک تعیین کرد.
کاربرد روان کننده های چرخ دنده
برای روان کاری چرخ دنده ها می توان روش هایی متنوع راب به کاربرد، ولی روش روان کاری چرخ دنده ها عمدتا به سرعت شان بستگی دارد. برای روان کاری چرخ دنده های با سرعت پایین معمولا از روش های ترشحی استفاده می شود در حالی که معمولا برای روان کاری چرخ دنده های سرعت بالا سیستم های روان کاری تحت فشار به کار می روند.
سیستم های روان کاری ترشحی
این نوع سیستم های روان کاری ساده ترین روش روان کاری هستند، ولی دامنه کاربرد شان به سیستم های چرخ دنده با سرعت خط گام حدود 1000 متر بر دقیقه محدود می شوند. در این روش قسمت هایی از چرخ دنده در داخل محفظه روغن به حرکت در آید و در روغن غوطه ور می شود. چرخ دنده مقداری از روغن موجود در ظرف روغن را با خود به همراه می برد. معمولا باید تا 2 برابر ارتفاع دندانه ها در داخل روغن قرار گیرد. در این روش روغن برداشته شده به کمک دندانه ها به محل درگیری دندانه ها و جاهای دیگر نیز منتقل می شود.
سیستم های روان کاری تحت فشار
اگر سرعت خط گام چرخ دنده ها بالای 1500 متر بر دقیقه باشد، از سیستم های روان کاری تحت فشار استفاده می شود. در این روش روغن کشیده شده از محفظه روغن با پمپاژ و از مسیر فیلتر، مبدل حرارتی و شیر فشار شکن به شکل تحت فشار به تجهیزات و چرخ دنده ها تغذیه می شود. روغن به کمک یک چند راهه و از نازل ها به شکل افشانه روی چرخ دنده ها پاشیده می شود.
جنس چرخ دنده ها
فولاد رایج ترین ماده مصرفی در ساخت چرخ دنده های صنعتی است. از روش های مختلف برای سخت کاری و دست یابی به مقدار سختی لازم در چرخ دنده ها استفاده می شود. تفاوت مقدار کربن موجود در فولادها اندازه سختی آنها را تعیین می کند.کربوریزاسیون، نیتراسیون و سخت کاری های حرارتی(القایی) از روش های اصلی در سخت کاری فولاد ها هستند. در میان مواد غیر آهنی، برنز شایع ترین فلز مصرفی در تولید چرخ دنده هاست. این نوع چرخ دنده ها غالبا به علت عدم تجانس تحت بار و تماس های لغزشی تغییر اندازه و حالت نمی دهند و در سیستم های چرخ دنده تحت دما به کار می روند. معمولا، چرخ دنده های برنجی در سیستم های انتقال قدرت و گیربکس ها نقش جان فدا را ایفا می کنند.
روان کاری و علل خرابی ها در چرخ دنده ها
هنگام تعیین علل خرابی های چرخ دنده ها باید بین خرابی های اولیه و ثانویه تمایز قابل شد. برای مثال خوردگی سوزنی یا خراش ممکن است موجب تخریب دندانه های یک چرخ دنده و ایجاد تنش ها و نیروهای مکانیکی و به دنبال آن شکستگی دندانه ها در اثر پدیده خستگی خمشی شود. در این حالت، خستگی خمشی پیامد ثانویه است و مستقیما به روان کاری و کاستی های آن مرتبط نمی شود، در حالی که خوردگی سوزنی یا خراش خرابی یا ایراد نوع اولیه است.
خوردگی سوزنی
پدیده مخرب خوردگی سوزنی به ایجاد ترک در سطح دندانه های چرخ دنده و یا در عمق کم(زیر سطح) آنها گفته می شود. معمولا ترک در فاصله ای کوتاه، موازی با سطح دندانه، قبل از تغییر جهت یا شاخه شدن به سطح تکثیر می شود. با رشد و توسعه ترک ها، تکه ای از سطح فلز از سطح دندانه چرخ دنده جدا می شوند. و حفره یا گودال تشکیل می شود. نتیجه تشکیل چند حفره با هم و رشد آنها ایجاد حفره ای بزرگ خواهد بود. این پدیده غالبا به شکل پوسته پوسته شدن سطح دندانه ها بروز خواهد کرد. (شکل ذیل).
وجود آلودگی و آب در روان کننده ها(به خاطر وجود هیدروژن)عامل افزایش روند خوردگی سوزنی است. تراشه های فلزی و ذرات حاصل از سایش موجود در روغن نیز با خط انداختن بر سطوح دندانه ها، تمرکز تنش و پاره شدن فیلم روغن سبب خوردگی سوزنی می شوند.
با روش های مختلف باید از بروز مشکل خوردگی سوزنی جلوگیری کرد. با کاهش تنش در نقطه تماس، از راه کاهش بار، تولید ترک و بروز خستگی به حداقل خواهد رسید. جنس چرخ دنده ها و کیفیت سطوح دندانه آنها نیز بر خوردگی سوزنی تاثیر می گذارد. اگر سطوح به دقت ماشین کاری و به شکلی مناسب تحت عملیات حرارتی و سخت کاری قرار گیرند، وقوع خوردگی سوزنی در آنها کاهش خواهد یافت.
خوردگی های سوزنی بسیار ریز
در چرخ دنده هایی که سطح شان سخت کاری شده باشد (با روش های کربوریزاسیون، نیتراسیون، سخت کاری القایی و سخت کاری با شعله) خوردگی سوزنی ممکن است در مقیاس کوچک تری رخ دهد و به طور نمونه ابعاد آن به 10 میکرون برسد. از لحاظ ظاهری و بصری، محل هایی که در آن ها خوردگی سوزنی رخ داده مات دیده می شوند. مات شدن امری کلی و عمومی در بروز پدیده خوردگی سوزنی بسیار ریز است.
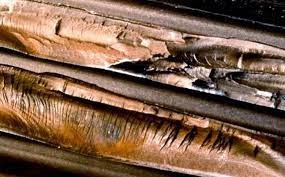
اختلاط قسمت های مختلف با یکدیگر
سایش های از نوع به هم آمیخته نسبتا ملایم اند و به تشکیل لایه های اکسید روی سطوح دندانه های چرخ دنده ها محدود می شوند. با این حال، اگر لایه های اکسید از هم گسیخته و آلیاژهای یاتاقان ها نمایان شوند، انتقال آنها به شکل ساییدگی های به هم آمیخته شدید بروز خواهد کرد. سایش های غیر طبیعی سطوح خراشیدگی نامیده می شوند. چرخ دنده هایی که در سرعت پایین و بارهای بالا کار می کنند بیشتر مستعد سایش های غیر طبیعی هستند، زیرا در این حالت روان کننده ها در شرایط روان کاری مرزی یا مخلوط عمل می کنند. در چرخ دنده های با سرعت پایین، افزایش ویسکوزیته روان کننده ها باعث کاهش سایش های به هم آمیخته سرعت پایین خواهد شد. وجود مواد افزودنی فشار بالا(EP) و ترکیبات فعال(گوگرد و فسفر) در روان کننده های مصرفی در چرخ دنده های سرعت پایین که تحت بارهای بسیار زیاد کار می کنن سبب افزایش سایش خواهد شد.
سایش های چسبی
ساییدگی های چسبی در چرخ دنده ها به علت کثیف شدن روغن با ذرات سخت و نوک تیز رخ می دهند. لجن در چرخ دنده ها با تولید داخلی، نفوذ گرد و غبار از هواکش ها، آب بندها و یا ورود طی مرحله تعمیر و نگه داری ایجاد می شود. ذرات تولید شده در داخل مجموعه چرخ دنده ها ذرات ساییده شده در داخل سیستم اند و سایندگی خاص دارند زیرا هنگام گیر افتادن در میان دندانه های درگیر بسیار سخت می شوند. ماسه های ساینده و ذرات آلودگی می توانند از هواکش ها و آب بندها نیز به داخل سیستم نفوذ کنند. وقوع سایش ناشی از آلودگی های خارجی و پس مانده های حاصل از سایش در چرخ دنده ها شایع است.
هنگام بازرسی سطوح دندانه های چرخ دنده ها، سایش های چسبی به شکل خراشیدگی نمایان می شوند. استفاده از فیلتراسیون، در مواقعی که سیستم های سیرکولاسیون روغن به کار می روند، سبب کاهش قابل توجه ذرات آلاینده نفوذی به روان کننده ها خواهد شد. با استفاده از آب بندی های روغنی مناسب و سیستم های تهویه فیلتر دار، مقدار آلودگی های نفوذ و فرو برده شده به سیستم چرخ دنده ها به حداقل خواهد رسید.
خراشیدگی
خراشیدگی هنگام روان کاری چرخ دنده ها در شرایط مرزی رخ می دهد. اگر ضخامت لایه روغن برای جلوگیری از تماس فلز با فلز کافی نباشد، فیلم اکسید روغن که معمولا از سطوح چرخ دنده ها محافظت می کند پاره خواهد شد.در این حالت ممکن است آلیاژهای سطوح یاتاقان ها به سطوح دیگر جوش بخورند و از سطح یاتاقان جدا شوند که نتیجه آن خسارت دیدن فاجعه بار چرخ دنده ها و دندانه های ان ها خواهد بود.ایجاد جوش های سخت روی سطوح دندانه های چرخ دنده ها ناشی از گرمای اصطکاکی بسیار بالاست. با ملاحظه سطوح چرخ دنده ها، انتقال مواد از یک سطح به سطح دیگر دیده خواهد شد.
اگر سطوح چرخ دنده های نو طی راه اندازی اولیه نرم و صیقلی نشده باشند، آسیب های اعمالی بر آنها به مراتب بیشتر خواهد بود. ترکیبات و مواد افزودنی حاوی فسفر و گوگرد مصرفی در روان کننده ها مواد افزودنی ضد خراشیدگی هستند. این مواد با انجام واکنش های شیمیایی با سطوح چرخ دنده ها(در نقاط موضعی دما بالا) از لایه اکسید روغن محافظت می کنند. لایه های سولفید آهن و فسفات در تماس های دما بالا در حالت جامد روی سطوح دندانه های چرخ دنده ها باقی می مانند. علائم خوردگی چرخ دنده ها مشابه با علائم خراشیدگی در آنها هستند.
ساخت چرخ دنده ها با سرعت بالا، نصب صحیح، نگه داری و تنظیم دقیق آنها خطر و احتمال بروز خراشیدگی ها را کاهش خواهد داد. با پایین نگه داشتن دمای روان کننده ها به کمک مبدل های حرارتی، در حالتی که از سیستم های گردش روغن استفاده می شود، خراشیدگی به حداقل خواهد رسید. استفاده از فولاد های نیتراته برای به حداکثر رساندن مقاومت در مقابل خراشیدگی توصیه شده است. در صورت امکان بروز خراشیدگی، نباید از فولاد های ضد زنگ و آلومینیوم برای تولید و ساخت چرخ دنده ها استفاده کرد.
جریان پلاستیک سطوح در دندانه های چرخ دنده ها
تغییر شکل چرخ دنده ها به علت بارهای سنگین مقاومت سطوح فلزی را به محدوده و حد الاستیکی می رساند. این پدیده معمولا در فلزات نرم تر رخ می دهد. در این حالت ممکن است سطوح دندانه ها در قسمت انتها و یا در امتداد نوک دندان ها به شکل بر آمده(لبه دار یا پله کرده) در آیند.
تجزیه و تحلیل ذرات حاصل از سایش در روان کننده های چرخ دنده
ذرات حاصل از سایش هنگام حرکت لغزشی دندانه های چرخ دنده ها از نوع سایشی مالشی هستند.(تصویر پایین). قطر این ذرات 10 تا 15 میکرون است و شکلی خطی و ملایم و سطحی نرم و صاف دارند. طی آغاز به حرکت کردن چرخ دنده های نو، ذرات حاصل از سایش بزرگ تر از ذرات سایشی حاصل از مالش اند و سازو کار تولیدی متفاوت تر دارند. تمام سطوح ماشین کاری شده خشن و زیر هستند. موقعی که سطوح سخت تر روی سطوح نرم تر می لغزند، بلافاصله ذرات سطوح نرم تر می شکنند و یا تغییر شکل می دهند. رفتار بسیار شکننده و تغییر شکل سطح سبب تولید ترک های نرم(حاصل از سایش) می شود. هرچه این سطوح یکنواخت تر باشند، سایش در آن ها نیز طبیعی تر خواهد بود. آهنگ کنار زدن زبری ها و تراشه ها فرآیند لغزش و سازو کار حذف آنها به زبری سطح اولیه، بار اعمالی و خواص مکانیکی آنها بستگی دارد.
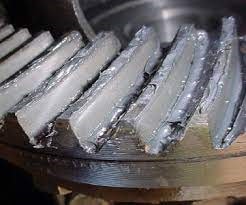
سایش های ناشی از برش
سایش های ناشی از برش هنگامی رخ می دهند که سطوح و یا ذرات سخت در سطوح نرم تر نفوذ کنند. در این صورت با حرکت سطوح روی هم،سطح نرم تر ورقه ورقه می شود و ذرات برشی و پلیسه مانند تولید خواهد شد.چرخ دنده هایی که در بارهای بالا و سرعت های پایین کار می کنند در معرض صدمه ناشی از ذرات آلودگی هستند، زیرا روان کاری آنها در شرایط روان کاری مرزی انجام می شود. سختی و اندازه ذرات سازنده در آهنگ سایش سطوح چرخ دنده ها و اندازه ذرات ساییده شده تولیدی اهمیت فراوان دارد(تصویر زیر)
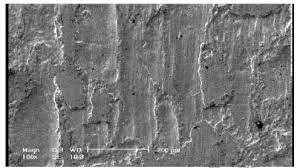
سایش ناشی از خستگی
به علت تکرار غلتش روی دایره گام چرخ دنده ها، یک ناحیه نوار مانند، مسطح و نرم روی دندانه آنها تشکیل می شود. سازو کار تولید این گونه سایش ها بر مبنای تشکیل و رشد هسته های ترک است. ترک ها در سطح دندانه ها تشکیل و موازی با سطح تکثیر و منتشر می شوند. در نهایت موقعی که این ترک ها به سطح منتشر می شوند. در نهایت موقعی که این ترک ها به سطح می رسند، در نواحی ضعیف و خاص موجب تشکیل صفحات سایش نازک و دراز می شوند. این سازو کار سایش پوسته ای(لایه لایه شدگی) نیز نامیده می شود. ضخامت و ابعاد ناحیه ساییدگی را ترک های زیر سطح کنترل می کنند که آنها نیز تحت کنترل بار اعمالی بر سطح هستند. نوار باریک و صفحات کوچک ناشی از سایش(لامینرها) هنگامی تولید می شوند که ذرات حاصل از سایش در میان دندانه های درگیر چرخ دنده های درگیر چرخ دنده ها گرفتار می شوند. این ذرات غالبا حفره های فراوان دارند و اندازه شان 20 تا 50 میکرون است(تصویر زیر)
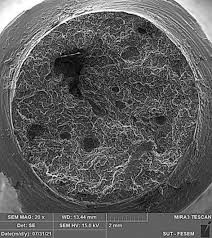
ذرات اکسید سیاه
طی فرایند ایجاد خراش، موقعی که فیلم روغن برای جلوگیری از تماس فلز با فلز کافی نباشد،لایه اکسید محافظت کننده روی سطوح چرخ دنده ها گسسته می شود و ممکن است آلیاژهای سطوح یاتاقان ها به هم جوش بخورند و انسجام خود را از دست بدهند. موقعی که این اتفاق می افتد، ذرات اکسید به علت گرمای زیاد تولید شده طی جوش خوردن و گسیخته شدن سطح تولید می شوند.(تصاویر زیر)
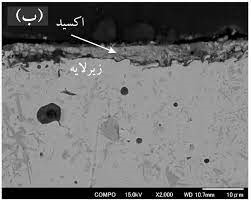
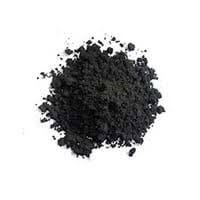
ذرات اکسید قرمز (زنگ)
ذرات اکسید قرمز موقعی در سیستم چرخ دنده ها تولید می شوند که آب یا رطوبت در روان کننده ها وجود داشته باشد. در صورت ملاحظه ذرات اکسید قرمز طی فرآیند تجزیه و تحلیل ناشی ذرات سایشی، توصیه شده است که آزمون اندازه گیری مقدار آب برای روان کننده ها انجام شود.
سیستم های انتقال قدرت و جعبه دنده ها با مجموعه ای از مشکلات و نارسایی ها در زمینه روان کاری و روان کننده ها روبرو هستند که برای رفع انها باید راه کارهای مختلف ارایه کرد که هر یک ریشه و ذاتی منحصر و خاص دارند و سبب تولید آلودگی و ذرات سایشی خاص می شوند.پایش وضعیت کارکرد چرخ دنده ها به روش تجزیه و تحلیل روغن روشی بسیار کارآمد و قوی برای شناسایی سایش های شدیدو خسارت بار است. با تجزیه و تحلیل زبری های حاصل از سایش می توان ریشه های تخریب و فساد را در سیستم های انتقال قدرت(چرخ دنده ها)تشخیص داد.