سطوح کارایی روغن های هیدرولیک
سطوح کارایی روغن های هیدرولیک
مقدمه
واژه « هیدرولیک » از کلمه یونانی (HUDRAULIKÓS) به معنی « چیزی که اجزای آبی دارد » بر گرفته شده است. دلیل این نامگذاری، پیشینه استفاده از آب در انتقال نیرو است. « بلز پاسکال» در سال 1650 میلادی آزمایشی را که به « بشکه پاسکال» معروف است ترتیب داد، ثابت کرد که اولا فشار هیدرو استاتیک به طور مستقیم با اختلاف ارتفاع رابطه داد، و ثانیا « فشار وارد بر یک سیال محصور شده و بدون جریان، بدون کاهش به تمام نقاط آن منتقل می شود »
بدین ترتیب بلز پاسکال پایه و اساس سیستم های هیدرولیک را که قادرند نیرو را در هر جهتی منتقل کنند بنا نهاد و نیز توانست پرس هیدرولیک معروف خود را اختراع کند. او در این دستگاه از آب به عنوان سیال هیدرولیک استفاده کرد. با وجود مزیت های متعدد سیستم های هیدرولیک، استفاده صنعتی از آن سال های طولانی زمان برد. در این بین، تلاش های ژوزف براما (1748-1814) و ویلیام آرمسترانگ (1810-1900) در توسعه پرس هیدرولیک نقش بسزایی داشته است.
تاریخچه توسعه روغن های هیدرولیک
تا دهه 1910، آب تنها سیالی بود که در سیستم های هیدرولیک به کار گرفته می شد. کشف خواص روان کاری و مزیت های روغن های معدنی، علاقه زیادی به استفاده از آن در سیستم های هیدرولیک به وجود آورد. با وجود طراحی پمپ های هیدرولیک مناسب، این صنعت به آب بندهای مناسب خود نیز احتیاج داشت. لذا اختراع الاستومرهای مصنوعی(لاستیک های نیتریل) در دهه 1930 راه را برای ساخت سیستم های هیدرولیکی قابل رقابت با مکانیزم های انتقال قدرت مکانیکی و الکتریکی هموار ساخت.
شاید در ابتدا روغن های پایه، به تنهایی نیاز سیستم های هیدرولیک را برآورده می کردند. اما دستگاه هایی طراحی و ساخته شد که برای بالا رفتن راندمان، به فشار و دمای کاری بالاتری نیاز داشت که علاوه بر طول عمر بیشتر، از تجهیزات و المان های این سیستم ها(همچون پمپ، سیلندر، سوپاپ ها و ... ) در مقابل خوردگی محافظت نماید. این گونه بود که برای اولین بار در سال 1940 روغن های هیدرولیک با مواد افزودنی( برای مقابله با اکسید شدن روغن و خوردگی قطعات) به بازار معرفی شد. مزیت های ذاتی سیستم های هیدرولیک، در کنار پیشرفت هایی که در توسعه این تجهیزات(از جمله سیالات هیدرولیک) به وجود آمد، باعث شد که صنایع مختلفی از جمله معدن و فولاد با شتاب بیشتری به استفاده از آن روی آورند. بدین ترتیب طراحی های جدید سیستم های هیدرولیک به سیالاتی با خواص بهبود یافته ضد سایش نیاز پیدا کردند. اولین نسل از این روغن ها در دهه 1960(که در استاندارد ISO تحت نام HM شناخته می شد) ساخته شد، و بلافاصله پس از آن روغن هایی با سیالیت بهبود یافته(HV) به بازار عرضه گردید.
با برجسته شدن مسائل زیست محیطی، بویژه از دهه 1990 که در دسترس بودن روغن های زیست تخریب پذیر مورد توجه قرار گرفت، پژوهش ها در این صنعت به سمت رفع نگرانی های محیط زیستی و سلامت روغن های هیدرولیک معطوف شد.
وجود استاندارد هایی که به انتخاب سیال هیدرولیک مناسب و آزمودن کارایی آن بیانجامد، یکی از نیازهایی بود که با گسترش این صنعت به وجود آمد. برای این منظور، سازمان های متعددی با جهت گیری های مختلف شکل گرفتند:
* کمیته های بین المللی استاندارد سازی، مانند ISO و DIN
* تولید کنندگان سیستم های هیدرولیک، ماشین آلات راه سازی و غیره، به عنوان مصرف کنندگان سیالات هیدرولیک
* تولید کنندگان قطعات مانند دنیسون و رکسروت
* سازمان های دولتی که بیشتر بر نیازهای صنایع نظامی و مسائل زیست محیطی تاکید دارند.
در این مقاله به بررسی سطوح کیفی ارائه شده در استاندارد های DIN و Denison می پردازیم.
سطوح کارایی – استاندارد DIN
موسسه استاندارد DIN سازمانی بین المللی در برلین آلمان است گه از سال 1917 تاکنون حدود 30.000 استاندارد را برای پوشش تمامی حوزه های تکنولوژی تدوین کرده است. در استاندارد DIN 51524 سیالات هیدرولیک با پایه روغن های معدنی از نظر سطوح کیفی به سه دسته اصلی تقسیم می شوند. همچنین هر سطح کیفی دارای 8 درجه گرانروی است که بر اساس ویسکوزیته در دمای 40 درجه سانتی گراد طبقه بندی می گردد.
در DIN 51524-Part 1 روغن هایی که تنها در برابر اکسید شدن مقاومت داشته و از خوردگی قطعات جلوگیری می کنند(R&O) قرار می گیرد. به این دسته از روغن ها کد HL اختصاص یافته است. در DIN 51524-Part 2 روغن هایی که علاوه بر ویژگی های HL دارای مواد افزودنی ضد سایش هستند قرار می گیرد که با کد HLP مشخص می شوند. DIN 51524-Part 3 به روغن های HLP اختصاص دارد که گرانروی آن ها بهبود یافته است که با کد HVLP شناخته می شود. بر خلاف روغن های HL و HLP، گرانروی این دسته تنها در دمای 40 درجه سانتی گراد مشخص شده و تعیین گرانروی صفر، 100 و همچنین 20- درجه آن به نظر تامین کننده تجهیزات واگذار شده است.
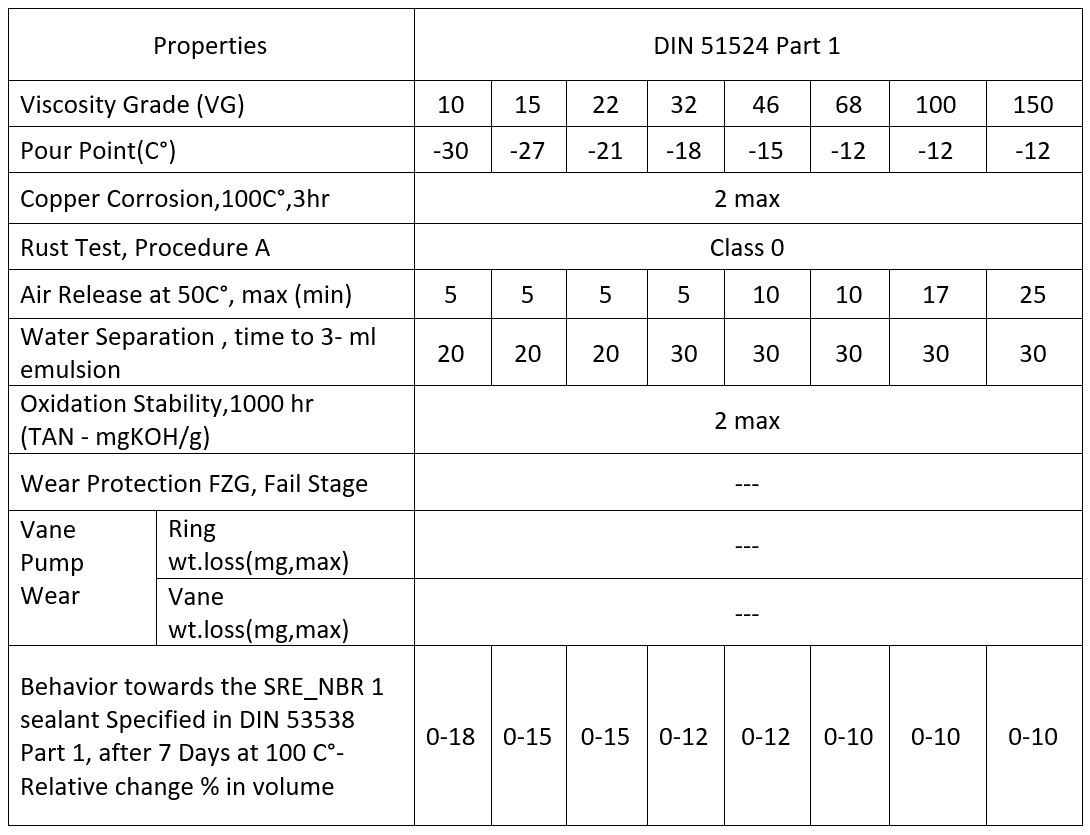
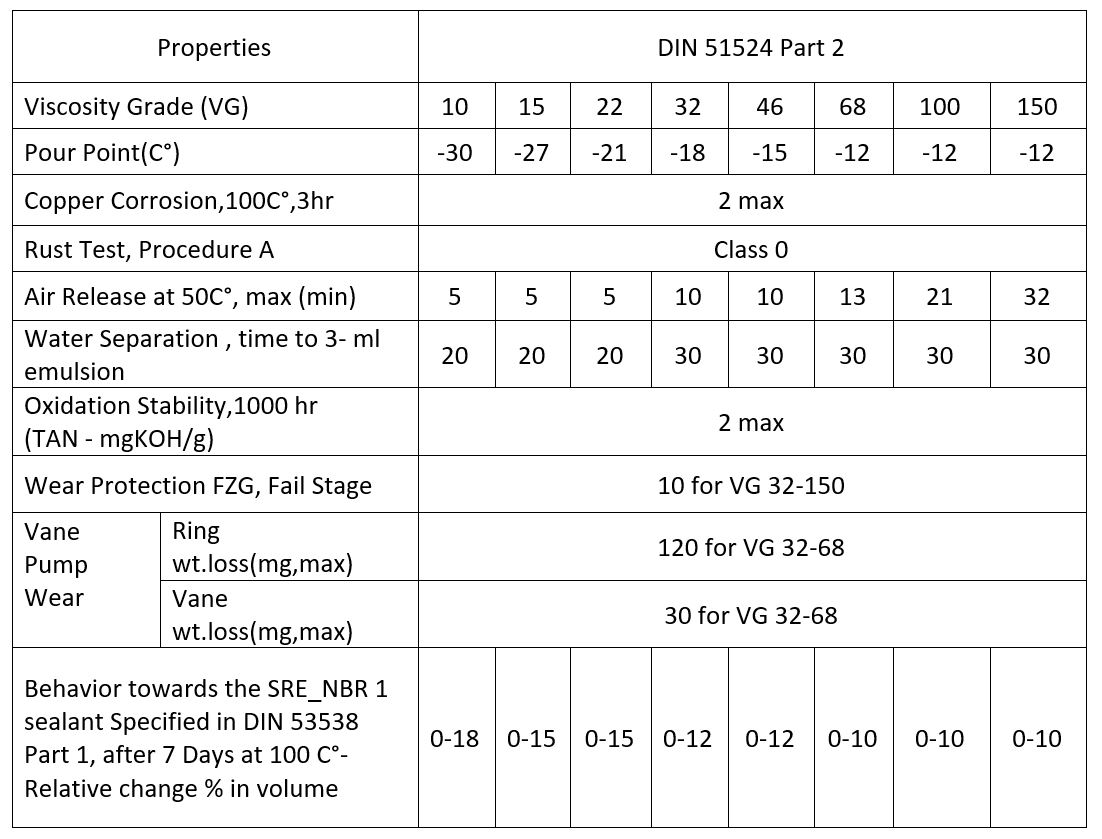
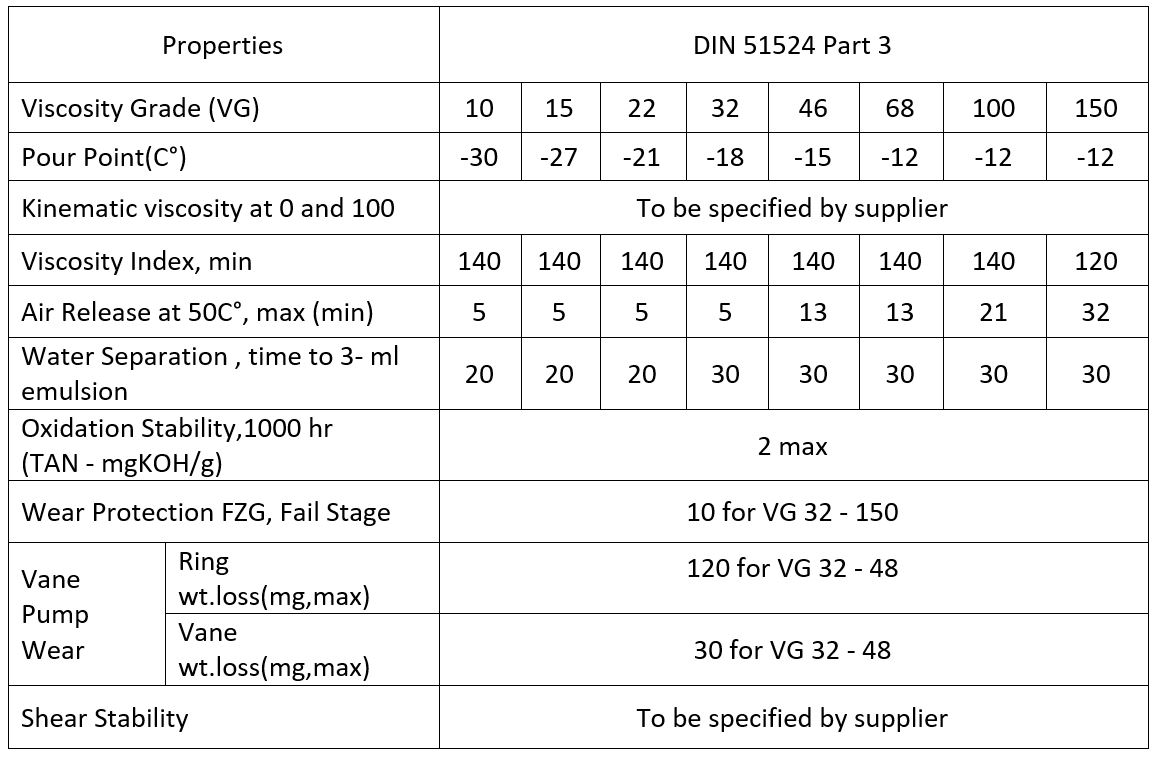
معیارهای لازم برای روغن های HL چندان سخت گیرانه نیست. با مخلوط کردن روغن های پایه گروه 1 یا 2 باحداقل مقدار مواد افزودنی آنتی اکسیدان و ضد خوردگی، می توان دو تست DIN 51585 (آزمون خوردگی برای 24 ساعت) و DIN 51587 (آزمون اکسید شدن برای 1000 ساعت) را با موفقیت گذراند. لیکن برای تهیه روغن های HLP بایستی از مواد افزودنی ضد سایش استفاده کرد. ترکیبات ZDDP معمولا بیشترین استفاده را برای این منظور دارند.
برای استفاده از ترکیبات ضد سایش، بایستی در محاسبه مقدار آنتی اکسیدان تجدید نظر کرد. چرا که این ترکیبات علاوه بر خواص ضد سایش، به عنوان یک آنتی اکسیدان هم عمل می کنند. البته نبایستی فراموش کرد که ترکیبات ZDDP مقاومت کمی در برابر هیدرولیز شدن داشته و نیز پایداری حرارتی آن ها کم است. در استاندارد DIN 51524 که معیار سایش بر مبنای تماس فولاد بر فولاد در نظر گرفته شده است، محدودیتی از این جهت وجود ندارد. لیکن در تهیه روغن هایی که می بایست با استاندارد های سازندگان تجهیزات هیدرولیک مطابقت کنند(مانند پمپ های Denison که در ساخت آن از آلیاژ برنز استفاده می شود، و یا تجهیزاتی که در بلبرینگ های آن نقره به کار رفته است) باید از ترکیبات ضد سایش دیگری استفاده کرد.
برای تهیه روغن های HVLP به پلیمر های بهبود دهنده شاخص گرانروی با پایداری برشی بالا نیاز داریم. پلیمرهای PMA این ویژگی را تامین می کند. علاوه بر این، به دلیل اینکه این نوع روغن در سیستم هایی با تنش هایی با تنش بالای برشی و حرارتی به کار می رود، انتخاب نوع مواد افزودنی بایستی به گونه ای باشد که در این شرایط، خاصیت خود را از دست ندهد. ویژگی های زیاد دیگری نیز وجود دارد که روغن های هیدرولیک بایستی دارا باشند. ویژگی های لازم برای روغن های HL و HLP در جدول 1 و برای روغن های HVLP در جدول 2 درج شده است.
سطوح کارایی- استاندارد Denison
در انتخاب روغن هیدرولیک مناسب باید به توصیه های سازنده تجهیزات توجه کرد. سازندگان مختلف، معیار های خاص خود را دارند. برای مشاهده این استاندارد ها باید به منابع معتبر مراجعه نمود. یکی از استاندارد های جامع و فراگیر توسط Denison ارایه شده است. شرکت Denison که در سال 1900 میلادی در اوهایو آمریکا پایه گذاری شده است، فعالیت خود را در صنعت هیدرولیک از سال 1925 آغاز نمود و در سال های قبل از جنگ جهانی دوم به تدوین استاندارد پرداخت. در این استاندارد HF-1 بیانگر روغن های نوع R&O است و معیارهای آن چندان تفاوتی با استاندارد DIN و ISO ندارد. روغن های HF-2 که خواص د سایش دارند، باید تست های ساییدگی پمپ های پره ای دنیسون، پایداری حرارتی CM، فیلتر شوندگی دنیسون و پایداری در برابر هیدرولیز شدن را با موفقیت بگذرانند. سطح کیفی HF-0 الزامات سخت گیرانه تری نسبت به HF-2 دارد که شامل گذراندن سایش پمپ پیستونی محوری دنیسون می شود. در کل می توان گفت که استاندارد Denison بیشتر به خاطر الزام ان برای پایداری حرارتی بالا و پایداری در برابر هیدرولیز شدن شناخته می شود. برخی معیارهای اصلی این استاندارد در جدول 3 آمده است.
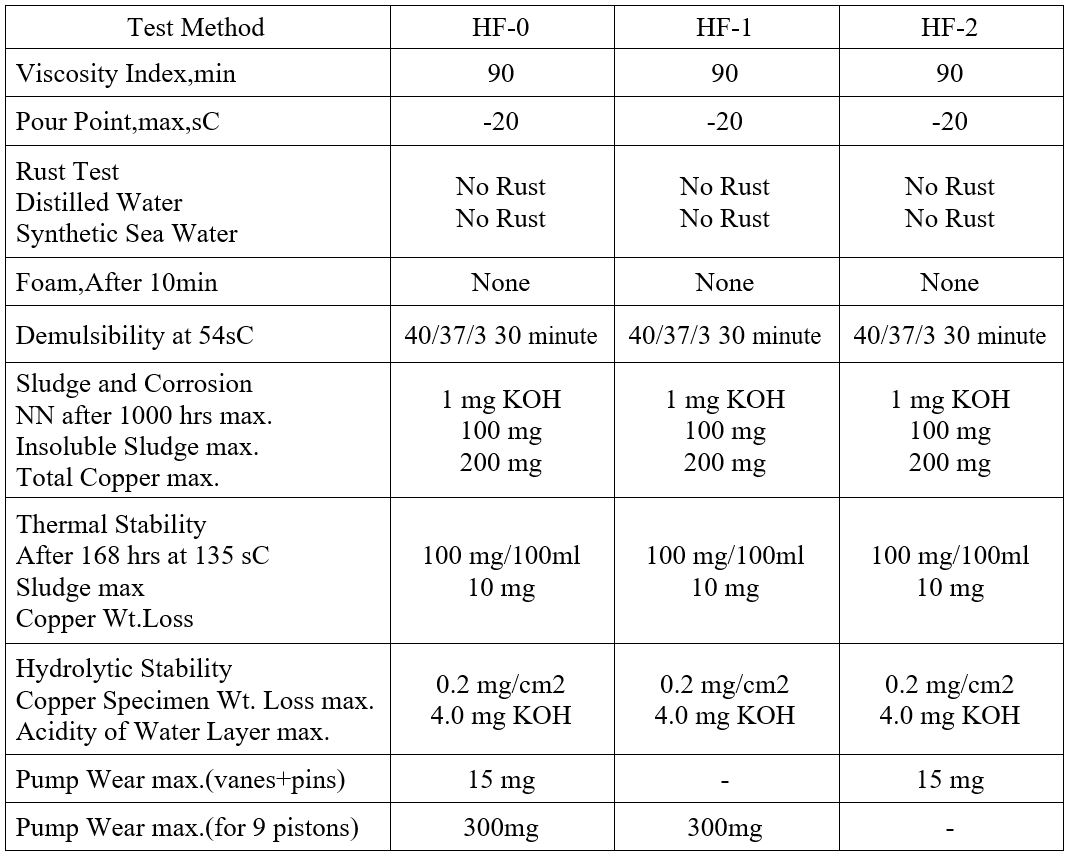
هر چند این الزامات محدودیت هایی در خصوص انتخاب روغن پایه و مواد افزودنی به وجود می آورد، این مکان وجود دارد که با انتخاب صحیح مواد افزودنی آنتی اکسیدان و ضد سایش، روغن هیدرولیکی تهیه کرد که پاسخگوی اغلب این معیارها باشد.
استاندارد Denison نسبت به DIN 51524 دارای معیار های بیشتری است. در این استاندارد میزان تشکیل لجن، پایداری حرارتی و پایداری هیدرولیتیکی نیز سنجیده می شود. لذا در طراحی پکیج های افزودنی این استاندارد باید ترکیباتی به کار رود که این معیارها را تامین کنند.
معیار پایداری هیدرولیتیکی و پایداری حرارتی عامل تعیین کننده ای برای انتخاب نوع ماده افزودنی ضد سایش در پکیج است. باید در نظر داشت که ترکیبات ZDDP پایداری حرارتی کمی دارند. این ترکیبات تا دمای 130 و حداکثر 170 درجه سانتی گراد مقاومت می کنند. لیکن این دما برای ترکیبات ضد سایش بدون خاکستر بالاتر از 200 درجه سانتی گراد است. با در نظر گرفتن اینکه این نوع ترکیبات قیمت و مقدار مصرف بیشتری دارند، انتخاب نوع مواد ضد سایش به معیارهای اقتصادی باز می گردد. در جدول 4 سه نوع ZDDP از نظر پایداری حرارتی، پایداری هیدرولیتیکی، خاصیت ضد سایش و قیمت با هم مقایسه شده اند.
در طراحی برخی پکیج های افزودنی، غلظت ترکیبات شیمیایی به گونه ای تعیین می شود که استاندارد های گسترده ای را تامین نمایند، که ممکن است مقدار آن ها بیش از مقدار مورد نیاز در برخی دستگاه ها باشد.لذا در صورتی که دستگاه مورد نظر استاندارد مشخصی( مثلاHF-0) را نیاز دارد، بهتر است از پکیج هایی که اختصاصا برای این سطح کیفی طراحی شده اند استفاده نماییم. معمولا در چنین مواردی غلظت مواد شیمیایی کمتر بوده و قیمت تمام شده کاهش می یابد.