آلودگی آب در روغن های روانکار
آلودگی آب در روغن های روانکار
به خوبی شناخته شده است که آلودگی ذرات در روغن با استفاده از یک کد ISO Cleanness می تواند منجر به بهبود و افزایش 10 تا 30 درصدی عمر قطعات حساس به آلودگی مانند شیرهای هیدرولیک، پمپ ها، یاطاقان ها و بلبرینگ ها شود. کد ISO Cleanness به عنوان اصلی ترین داده در اغلب نتایج آنالیز روغن صنعتی استفاده می گردد و مقدار این کد می تواند به تعیین پاکیزگی کلی سیستم تحت نظارت کمک کند که در این خصوص در مباحث آینده خواهیم پرداخت.
صنایع سالانه میلیون ها دلار صرف بهبود فناوری فیلتراسیون می نماید تا آلودگی ذرات در روغن را کاهش دهند، در حالیکه برخی از شرکت های پیشرفته تنها با کنترل و پایش وضعیت و آنالیز روغن میزان خرابی را تا 90 درصد کاهش می دهند. با این حال، در برخی صنایع و محیط ها، آب بسیار آلوده کننده تر از ذرات جامد است و اغلب به عنوان عامل اصلی خرابی اجزا نادیده گرفته می شود.
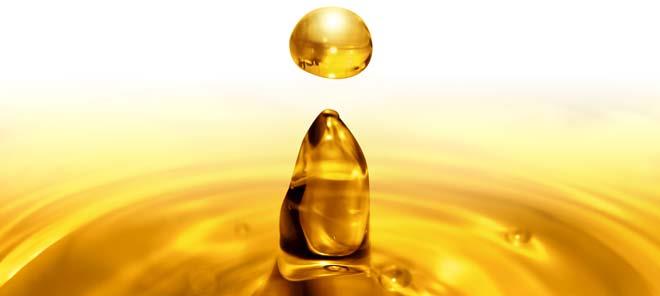
آب در روغن های روانکار
آب در روغن می تواند در سه حالت یا فاز وجود داشته باشد. حالت اول، معروف به آب محلول، که با تک تک مولکول های آب پراکنده شده در روغن مشخص می شود. آب محلول در یک روغن روان کننده قابل مقایسه با رطوبت هوا در یک روز مرطوب است. ما می دانیم که آب در آنجا وجود دارد، اما چون مولکول به مولکول بصورت پراکنده است، برای دیده شدن بسیار کوچک هستند.
به همین دلیل، یک روغن می تواند حاوی غلظت قابل توجهی از آب محلول باشد بدون اینکه نشان دهنده وجود آن باشد. بیشتر روغن های صنعتی مانند روغن هیدرولیک، روغن های توربین و ... بسته به دما و سن روغن می توانند از 200 تا 600 ppm (0.02 تا 0.06 درصد) آب در حالت محلول نگه دارند، در حالی که روغن های قدیمی قادر به نگهداری سه تا چهار برابر آب بیشتر از روغن نو در حالت محلول هستند.
هنگامی که مقدار آب در روغن از حداکثر مجاز برای حل شدن بیشتر شود، روغن اشباع می شود. در این مرحله ، آب بصورت قطرات میکروسکوپی معروف به امولسیون در روغن معلق است، که در این حالت روغن کدر خواهد شد. این شبیه به تشکیل مه در یک روز خنک و بهاری است، میزان رطوبت هوا از نقطه اشباع فراتر رفته و در نتیجه قطرات کوچک آب بصورت مه پدیدار می گردند.
افزودن آب بیشتر به مخلوط روغن – آب ایجاد دو فاز، یک لایه آب آزاد و همچنین روغن آزاد و یا امولسیون می شود. مثل، باران وقتی که مقدار رطوبت هوا بیش از حد می شود می بارد. برای روغن های معدنی و سنتزی PAO (Pol-alpha-olefin) که وزن مخصوص (Specific Gravity) آنها کمتر از 1.0 است، این لایه آب آزاد در کف مخازن یافت می شود.
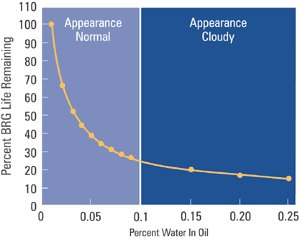
آثار آلودگی آب
در سیستم روانکاری، فاز مضر، آب آزاد و امولسیون (آب و روغن) هستند. به عنوان مثال در یاتاقان های ژورنال (Journal Bearing)، جدانشدن آب از روغن می تواند منجر به از دست رفتن لایه نازک (فیلم نازک روغن) روغن گردد که منجر به سایش بیش از حد می گردد. تنها یک درصد آب موجود در روغن می تواند طول عمر یاتاقان های ژورنال را تا 90 درصد کاهش دهد.
برای یاتاقان های نورد غلتکی (Rolling Element Bearings)، وضعیت بدتر است. آب نه تنها استحکام لایه روغن را از بین می برد، بلکه هر دو آب آزاد و امولسیون تحت دماهای بالا و فشارهای شدید ایجاد شده در ناحیه بار یاتاقان می تواند منجر به تبخیر آنی و ایجاد سایش فرسایشی شود.
تحت شرایط خاص در نتیجه فشارهای زیاد ایجاد شده در ناحیه بار یاتاقان، مولکول های آب می تواند به اتم های تشکیل دهنده خود، اکسیژن و هیدروژن تبدیل گردند. یون های هیدروژن تولید شده توسط این فرایند به دلیل اندازه کوچک خود می توانند بر روی سطح مسیر یاتاقان جذب و منجر به پدیده ای به نام شکنندگی هیدروژن یا تُردی هیدروژنی (Hydrogen Embrittlement) گردند.
تُردی هیدروژن ناشی از تغییر در متالورژی بلبرینگ های زیر سطحی است. این تغییر باعث می شود مواد یاتاقان ضعیف یا شکننده شده و مستعد ترک خوردگی در زیر سطح مسیر حرکتی شوند. هنگامی که این ترک های زیر سطحی به سطح گسترش می یابد ، نتیجه می تواند منجر به ایجاد ترک و شکاف گردد.
از آنجا که اثرات آب آزاد و امولسیون در مقایسه با آب محلول مضرتر است، یک قاعده کلی این است که اطمینان حاصل شود که سطح رطوبت بسیار کمتر از نقطه اشباع باقی بماند. سطح رطوبت یا میزان آب برای بیشتر روغن های در حال استفاده بسته به نوع روغن و درجه حرارت، بین 100 تا 300 ppm یا کمتر است.
با این حال، با توجه به میزان آب حتی در این سطوح می تواند منجر به مقدار قابل توجهی آسیب به تجهیزات گردد. به طور کلی، چیزی به نام آب بسیار کم وجود ندارد و باید تمام تلاش جهت پایین نگهداشتن آلودگی آب در روغن به کار بگیریم.
اثرات آب بر روانکار
آب نه تنها بصورت مستقیم بر اجزای ماشین تأثیر مخربی می گذارد، بلکه نقش مستقیمی نیز در میزان فرسودگی روغن های روان کننده دارد. وجود آب در یک روغن روان کننده می تواند روند اکسیداسیون را ده برابر نماید و در نتیجه باعث فرسودگی زودرس روغن به ویژه در حضور فلزات کاتالیزوری مانند مس، سرب و قلع می گردد.
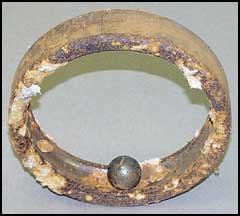
آب نه تنها بصورت مستقیم بر اجزای ماشین تأثیر مخربی می گذارد، بلکه نقش مستقیمی نیز در میزان فرسودگی روغن های روان کننده دارد. وجود آب در یک روغن روان کننده می تواند روند اکسیداسیون را ده برابر نماید و در نتیجه باعث فرسودگی زودرس روغن به ویژه در حضور فلزات کاتالیزوری مانند مس، سرب و قلع می گردد.
علاوه بر این، انواع خاصی از روغن های سنتزی مانند استرهای فسفات (Phosphate Esters) و استرهای دی بازیک (Diabasic Esters) با آب واکنش نشان داده و منجر به تخریب مواد پایه و در نهایت تشکیل اسید می شوند.
فقط روغن پایه نیست که می تواند تحت تأثیر آلودگی آب و رطوبت قرار گیرد. برخی از افزودنی ها مانند افزودنی های گوگردی AW و EP و آنتی اکسیدان های فنلی به آسانی توسط آب هیدرولیز می شوند، که منجر به از بین رفتن خاصیت افزودنی و تشکیل محصولات جانبی اسیدی می گردد.
این محصولات جانبی اسیدی می توانند باعث خوردگی سایشی شوند، به ویژه در اجزای حاوی فلزات نرم مانند آلیاژ بابیت (Babbitt) که با بلبرینگ ژورنال و اجزای برنز و برنجی استفاده می شود. سایر مواد افزودنی مانند دمولسیفایرها، مواد پخش کننده، مواد شوینده و بازدارنده های زنگ زدگی را که بوسیله رطوبت زیاد شسته و از بین می روند. این امر موجب تجمع لجن و رسوب، کثیف شدن فیلتر و ... می شود.
اندازه گیری آب
برای کنترل سطح رطوبت، ابتدا باید وجود آن را تشخیص دهید. پنج روش پایه آزمایش برای تعیین میزان آب و رطوبت روغن های روانکار وجود دارد. این روش ها از یک دستگاه ساده گرفته تا آزمایش شیمیایی پیچیده تر قابل انجام است. همچنین فناوری پیشرفته تری که معمولاً در آزمایشگاه های آزمون برای تعیین دقیق سطح آب در مقیاس ppm استفاده می شود.
اساسی ترین آنها روش Crackle Test است. در این آزمایش، یک صفحه داغ در دمای 130 درجه سانتی گراد (320 درجه فارنهایت) و یک قطره کوچک روغن در مرکز قرار می گیرد. هرگونه رطوبت موجود در روغن در تعداد حباب های مشاهده شده در هنگام بخار شدن آب مشاهده می شود. بسته به نوع روان کننده، حباب های نسبتاً کم تقریباً 500 تا 1000 ppm (0.05 تا 0.1 درصد) آب را نشان می دهند.
حباب های بیشتر با اندازه بزرگتر ممکن است نشان دهنده حدود 1000 تا 2000 ppm آب باشند، در حالی که صدای ترک خوردگی قابل شنیدن میزان رطوبت بیش از 2000 پی پی ام را نشان می دهد. Crackle Test فقط به آب آزاد و امولسیون حساس است.
آزمایش ساده دیگر که امکان انجام در محل را دارد، استفاده از سلول تحت فشار است که در آن نمونه با واکنش شیمیایی (هیدرید کلسیم) آماده، در ظرفی قرار داده شده و به شدت تکان داده می شود. تغییر فشار درون سلول برای تعیین وجود آب آزاد بررسی می شود.
سومین نوع آزمایش میزان آب، استفاده از سنسور رطوبت نسبی است. این سنسور از یک شبکه خازنی فیلم نازک استفاده می کند که می تواند میزان رطوبت را تعیین کند. این فناوری چه در هوا و چه در نفت یکسان است که در خروجی داده ها معمولاً با درصد RH (Relative Humidity) نمایش می دهند.
همانطور که قبلاً اشاره شد، درصد RH نشان دهنده این است که آیا روغن هنوز به نقطه اشباع رسیده است یا خیر، اگرچه همانطور که در اتمسفر(جو)، هرچه دما پایین تر باشد، نقطه اشباع از نظر غلظت آب کمتر است. در حالی که از نظر ریاضی می توان مقدار ppm را از درصد RH در برابر منحنی اشباع روغن در دمای مشخص بدست آورد. تفکر پشت این نوع سنسورها این است که مانند یک هشدار اولیه در مورد مشکلات قریب الوقوع فعال می گردد تا جهت صحت سنجی نمونه ای به آزمایشگاه آزمون ارسال گردد.
گذشته از روش های میزان آب در محل، یکی دیگر از روش های متداول میزان آب طیف سنجی مادون قرمز تبدیل فوریه (FTIR) است. این آزمایش نسبت به آب آزاد، امولسیون و محلول حساس است اما در قدرت تشخیص کمتر از 1000 ppm محدود می شود.
این برای برخی از برنامه های پایش و نگهداری کافی است، اما برای کاربردهای صنعتی کافی نیست. آزمایشگاه های فرآورده های نفتی مانند آزمایشگاه مشاوران آزمای نفت ایرانیان روشی استفاده می کنند که اغلب کمتر از 0.1 درصد حجم آب را نیز گزارش می دهند.
دقیق ترین روش برای تعیین میزان آب آزاد، امولسیون و محلول در یک روغن روانکار، تست میزان آب به روش کارل فیشر (Karl Fischer) است. هنگامی که این تست به درستی استفاده شود، می توان سطح آب را از 10 ppm یا 0.001 درصد تعیین کرد.
این روش هنگامی که باید غلظت دقیق تری از آب مشخص شود استفاده می شود. هنگام استفاده از روش کارل فیشر باید احتیاط گردد تا از اثرات تداخلی ناشی از افزودنی های گوگرد EP و AW جلوگیری شود.
از هر روشی که برای تعیین سطح آب استفاده می شود، یک چیز مسلم است: آب عامل اصلی خرابی روان کننده، خرابی قطعات و تضعیف اطمینان ماشین آلات است. مانند همه آلاینده ها ، نه تنها تشخیص وجود آن مهم است، بلکه اقدامات لازم برای کنترل یا حذف منبع نفوذ آب نیز ضروری است. در صورت امکان، سطح آب در تمام تجهیزات باید زیر حد اشباع و تا حد ممکن سطح رطوبت پایین نگه داشته شود.
این که آیا شما بخواهید از هواکش، پلمپ تجهیزات یا فیلترها در واحد صنعتی استفاده نمایید، خود موجب کاهش سطح آب در انواع تجهیزات خواهد شد و می تواند عمر روان کننده و ماشین آلات را به طرز چشمگیری افزایش دهد.
Noria Corporation
ترجمه: مرتضی بقائی – واحد مارکتینگ